Injection molding is used by manufacturers to produce plastic items. This process is used in mass-production i.e. for making hundreds if not thousands identical components in a short period of time. The fact that it allows companies to accelerate their production process and still create high-quality items is the main reason why injection molding is so widely utilized.
What does the process include?
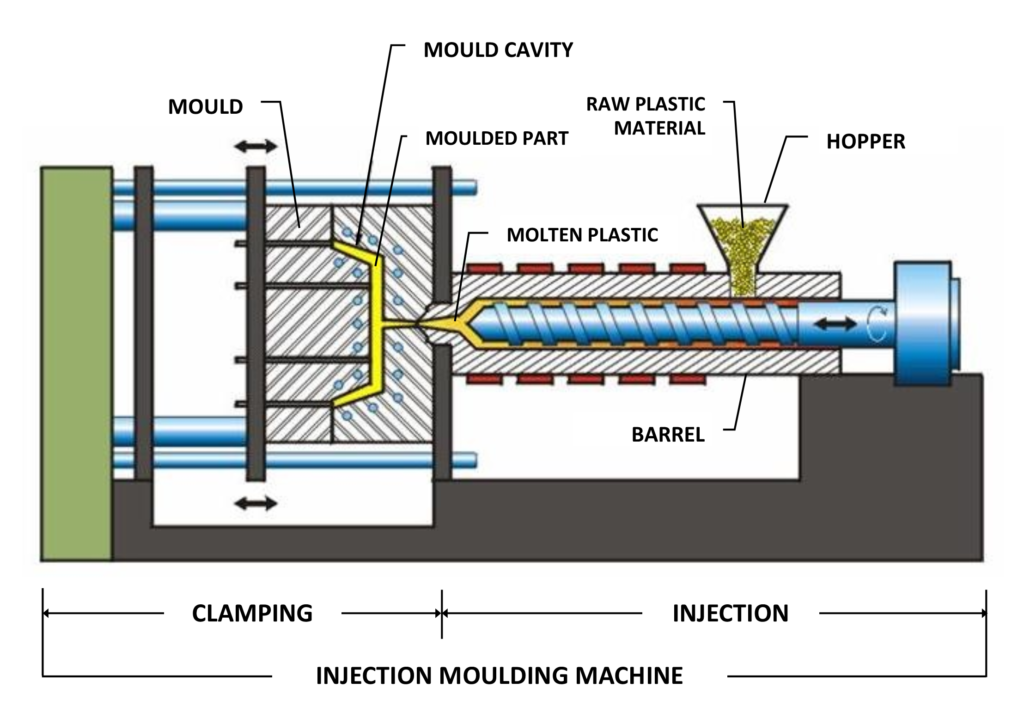
Firstly, we are going to try to explain to you how this process works. Obviously, the first thing a manufacturer needs is a mold that is going to shape the component. The great about today’s technology is that it allows people to design it digitally via CAD technology. Basically, this means that workers can create whatever they have envisioned, and most importantly, they can make as many changes as they need to until they have created a perfect frame.
Nowadays, companies can opt for 3D printing of plastic mold, but these come short in comparison to the metal ones. Why? Well, not only are the plastic ones less durable than metallic ones, but they also do not have the smooth finish that frames made of aluminum or steel have. This means that there might be some small indentation on the components that are produced using a 3D plastic cast.
Now that we have a mold, let’s discuss the injection molding process. When it comes to a thermoplastic that is most commonly used it includes – Polycarbonate PC, Polypropylene PP, Acrylonitrile-Butadiene-Styrene ABS, and Nylon PA. This plastic is added to a heated barrel when it is melted by high temperatures. Then, the liquid goes through a small pipe from the injection molding machine to a previously designed and tested frame. Upon filling the mold’s cavity, only few seconds are necessary for it to cool down and become solid. Once the component is finished, the cast ejects it and the entire process is repeated.
These are some basic information, but if you are intrigued by injection molding and want to learn what type of services professionals can provide you with, click here.
What are the advantages?
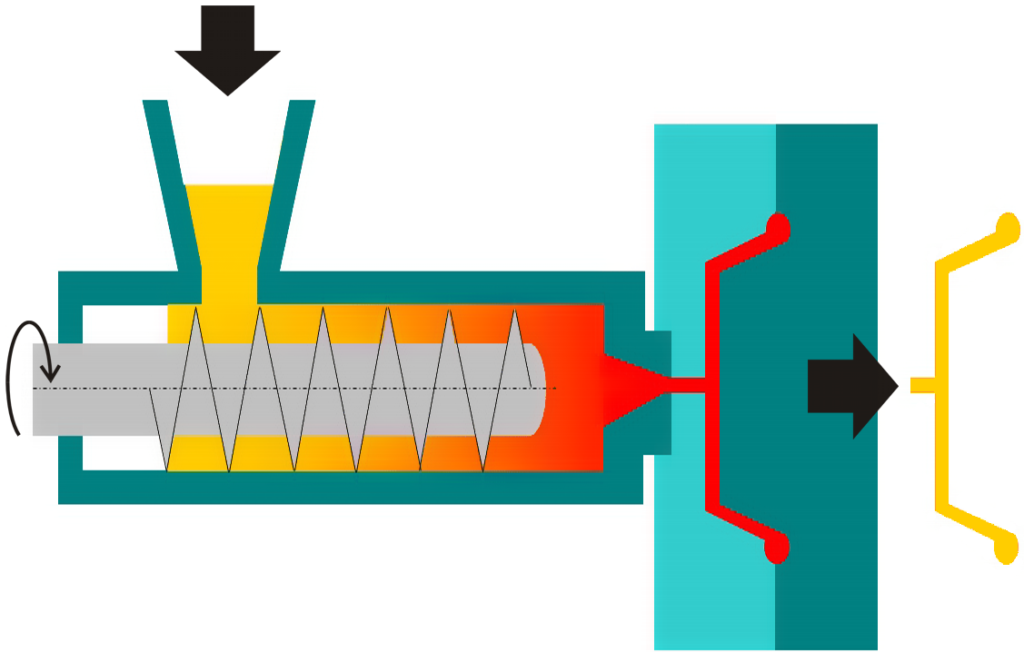
Now that we have told you how the entire process works, it is time to mention some of the benefits and reasons why so many companies around the world use it.
Intricate designs
One of the features of the injection molding process is that plastic is subjected to very high pressure, the highest when compared to other types of molding. Why is this important? Well, it simply means that this pressure allows you to create any design you want, regardless of its complexity.
Depending on the components you are working on, these can only be decorative, while, on the other hand, they can be an essential part of the item. The same thing also goes for different shapes, which you might not be able to manufacture otherwise.
Fast Production
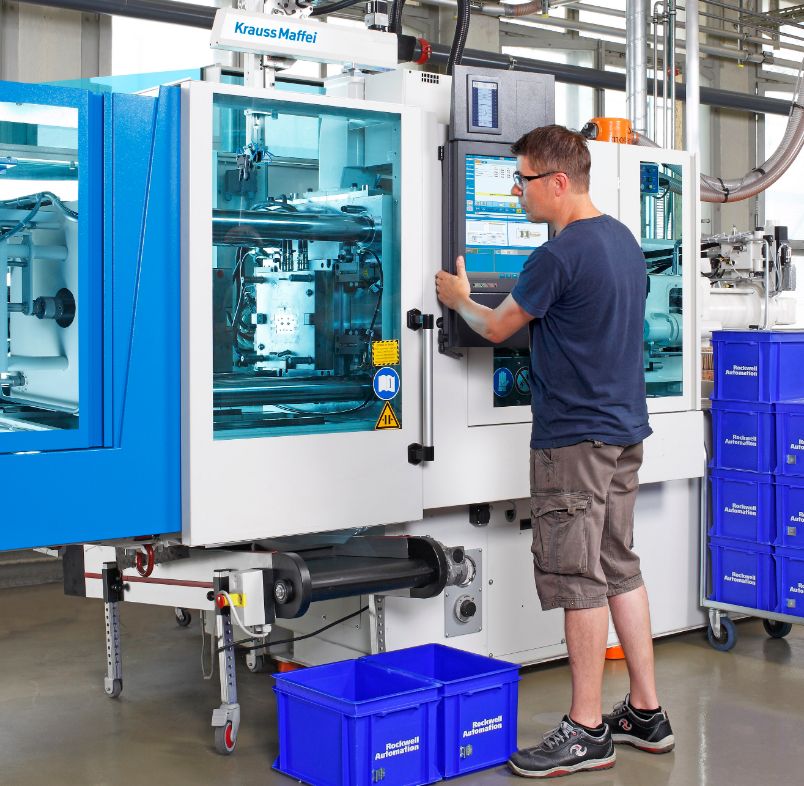
Besides being able to create whatever you want, being able to produce it quickly in thousands of samples is the next thing that you want. Without a doubt, injection molding is the most efficient process when compared to other similar ones.
The period between the two cycles is only between 15 and 200 seconds. This means that this machine allows manufacturers to produce more goods during a shorter period of time. Naturally, this means that they will have more components to sell thus increase their revenue.
Besides allowing companies to produce more and earn more money, it is also cost-effective because well, a single cycle doesn’t require a lot of time.
High-quality products
Each manufacturer wants to be certain that their products are of top quality, and injection molding allows them to be sure that that is the case. Clearly, depending on the type of component and its use some parts might need to be flexible while others have to be sturdy. This is something that companies need to know before starting the process so they would be able to make the right adjustments.
In addition, one can also add filler to the plastic which reduces its density, but also ensure that the component is of greater strength upon being made.
Flexibility
Another advantage is the companies can use and mix different materials. Clearly, the machine has to be programmed for it and by using co-injection molding one would be able to make components by combining two or more different types of plastic.
Is it really necessary to explain why this feature is so important to all manufacturers? Simply put, when it comes to designing and creating an item, one’s possibilities are endless. Mix and match materials and colors to get something that is one of a kind and that, clearly, meets all your client’s requirements.
Minimize waste
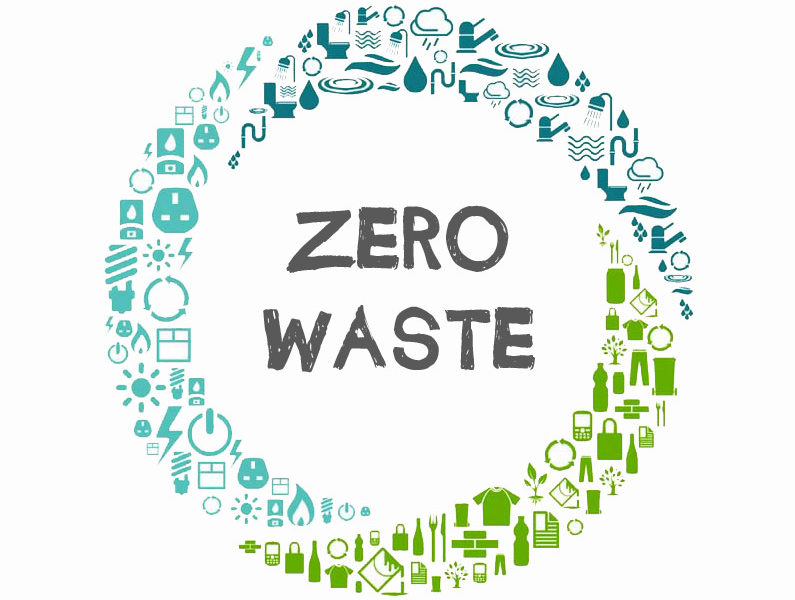
When looking for a company that uses injection molding, one should always investigate how they conduct their business. By this, we mean that those that have a green initiative should be carefully considered. Creating waste during any kind of manufacturing process is inevitable.
Depending on the technology and materials used, it can be in a larger or smaller amount. However, one should always go with companies that have found a way to recycle that waste i.e. those that have a plan on how to use it again.
First of all, this is not only beneficial for the environment, since there won’t be a need to use new materials and get rid of the old ones. Secondly, for the same reason, this is also a cost-efficient. The requirement of the materials is going to reduce which means that you will spend less money on it.
Reduced labor force
This final benefit that we are going to mention is an obvious one, since, as you can assume, this entire process is automated. What does this mean? Well, basically, it means that no manpower is required since a majority of the work is done by a computer and robotics technology.
This means that companies do not need many employees thus this is another aspect of the business where they can save a significant amount of money. What’s more, it even means that the chances of injuries and accidents happening are also quite reduced thus the safety of employees is increased.